Offsite construction, also known as prefabricated or modular construction, is on the rise in New Zealand as sustainability, efficiency and productivity increases are sought in the design and construction industry. Prefabricated panels, 3-D pods and even whole buildings are now being manufactured off site in a factory, then transported and then installed on site.
While offsite construction is a complementary system to traditional construction methods, there are some key differences regarding where and when LBPs are involved in the manufacturing and installation processes for offsite construction, particularly under the new voluntary modular component certification scheme recently introduced by the Ministry of Business, Innovation and Employment (MBIE).
The new scheme is called BuiltReady, and it will allow modular component manufacturers to be certified and registered to design and/or manufacture modular building components that will be deemed to comply with the Building Code. The scheme will allow in most cases for reduced inspections and faster, more consistent building consent applications, which will aid in reducing costs and on-site building time.
Scheme certification bodies will be responsible for certifying manufacturers. To ensure they are competent to perform this function, certification bodies must be both accredited by the accreditation body and registered with MBIE before they can perform functions under the scheme. Similarly, manufacturers must be certified by a certification body and registered with MBIE before they can utilise the scheme’s compliance pathways.
A certification body will evaluate a manufacturer’s policies, procedures, and systems to ensure that the design and/or manufacture of modular components is done competently and reliably to a standard that complies with the Building Code. These systems include an appropriate quality plan and quality management system, documented design and/ or manufacturing processes, employee and contractor systems including competency and training requirements, and complaints and disputes processes. Ongoing monitoring of a manufacturer will include regular third-party audits and installation inspections.
A registered manufacturer may issue manufacturer’s certificates for the modular components it produces that fall within its scope of certification. Building consent authorities (BCAs) must accept a manufacturer’s certificate as evidence that the specified modular component complies with the Building Code.
What is the BuiltReady scheme?
Under the BuiltReady scheme, the entire prefabricated construction process from design (where applicable), manufacture, assembly, transportation, and onsite installation of modular components will be assessed and certified. The following process flow diagram shows how the BuiltReady framework works:

BCAs will only inspect work that is not covered by a manufacturer's certificate. Examples of such work are foundations and site work, or other parts of the building not covered by a manufacturer's certificate.
How does the BuiltReady scheme work?
A manufacturer can apply for BuiltReady certification in one of two ways:
- design and manufacture – manufacture modular building components to a Building Code compliant design that the manufacturer has developed or adapted themselves, or
- manufacture only – manufacture modular building components to a Building Code compliant design.
Three types of modular components that can be certified are defined by the Building (Modular Component Manufacturer Scheme) Regulations 2022 and include:
- prefabricated frames and panels. These include open frames or trusses, or enclosed frames or panels. Examples include floor, wall and ceiling panels or cassettes, frame and truss, panelised building systems, and structural insulated panels (SIP panels). Prefabricated frames and panels may also include mechanical, electrical, or other systems.
- prefabricated volumetric structures. These are three dimensional products that comprise of one or more of the prefabricated frame or panel products described above. Examples include laundry and bathroom pods, and types of modular units. They may also include mechanical, electrical, or other systems.
- prefabricated whole buildings (ie the entire building is manufactured off site).
BuiltReady manufacturer’s certificates – a deemed to comply pathway
A registered manufacturer can issue a manufacturer’s certificate to accompany a building consent application and a second certificate to accompany a code compliance application.
For manufacturers certified to design and manufacture, the manufacturer’s certificate will cover both the design and manufacture of the modular component included in the building consent. For manufacturers certified to manufacture only, the modular component will be deemed to comply, but the building design still needs to be approved by the responsible BCA. Any building work not covered by a manufacturer’s certificate must still be approved by the BCA as per standard practice.
A manufacturer’s certificate issued for a code compliance certificate is a statement that the modular component has been designed (if applicable), manufactured, transported, stored, and installed according to the specifications provided in the initial manufacturer’s certificate (including any approved variations). Given that most offsite construction projects require traditional on-site works and installation, LBPs may encounter more ‘hybrid’ builds in the future and opportunities to learn how to install and integrate modular components.
Restricted building work
For traditional construction, any LBP who carries out restricted building work must provide a Certificate of Design Work or Record of Building Work. However, the Building (Definition of Restricted Building Work) Order 2011 has been amended to specify that the order does not apply to building or design work carried out by a registered manufacturer designing or manufacturing a modular component off site. All relevant records related to LBP work by a registered manufacturer will be part of the manufacturers’ own quality management systems, ensuring there is a record of building work for that building.
A Record of Building Work is still required for site works such as foundations/ subfloor framing and any work that falls outside what is specified in a manufacturer’s certificate. A Certificate of Design Work will be required if a manufacturer is certified to only manufacture modular components.
BuiltReady will be open for applications from manufacturers from mid-2023. A register of certified manufacturers will be available at www.building.govt.nz.
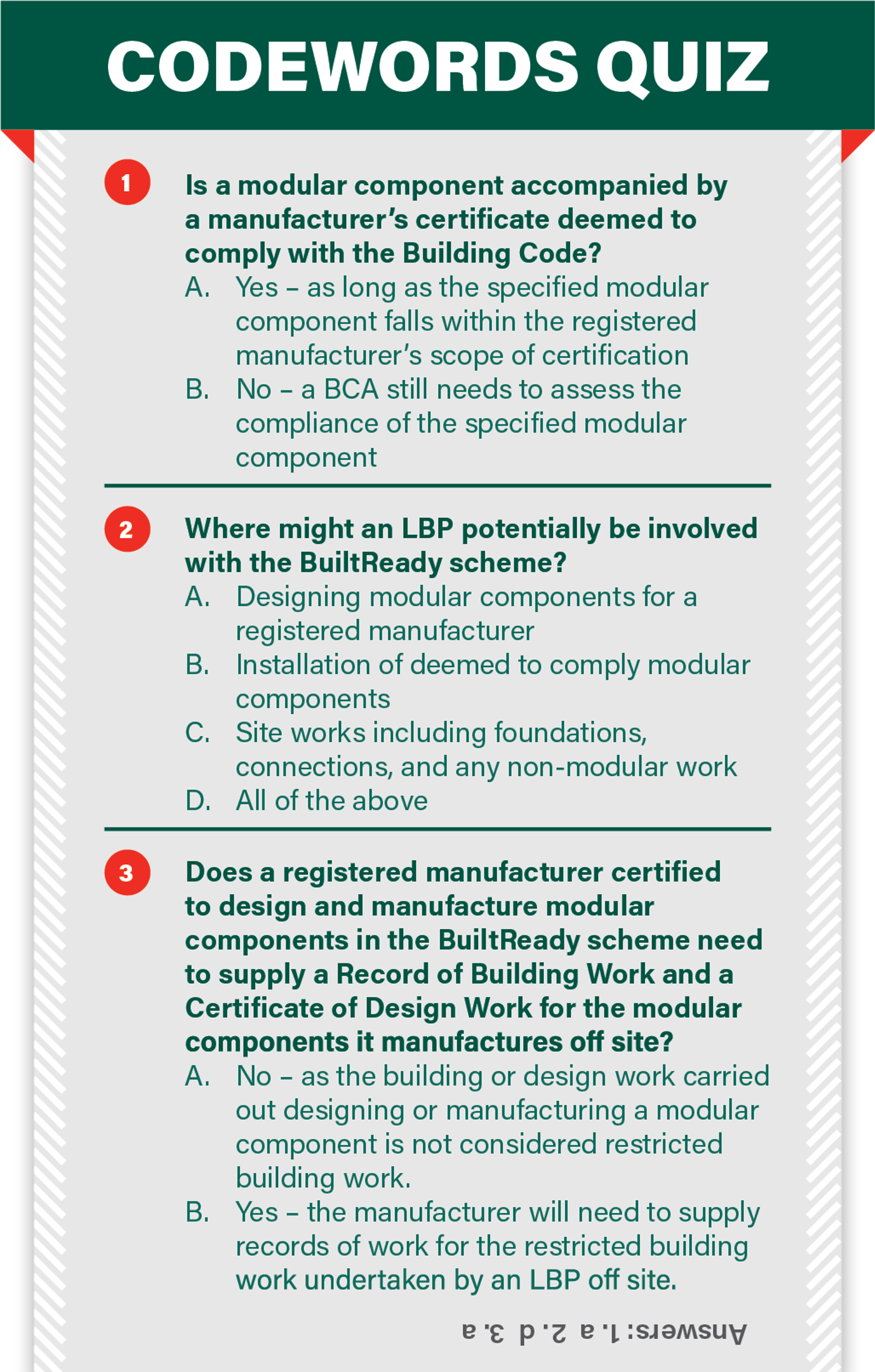
Where can I find more information?
The BuiltReady pages at www.building.govt.nz contain detailed information about the scheme including scheme rules and guidance material.