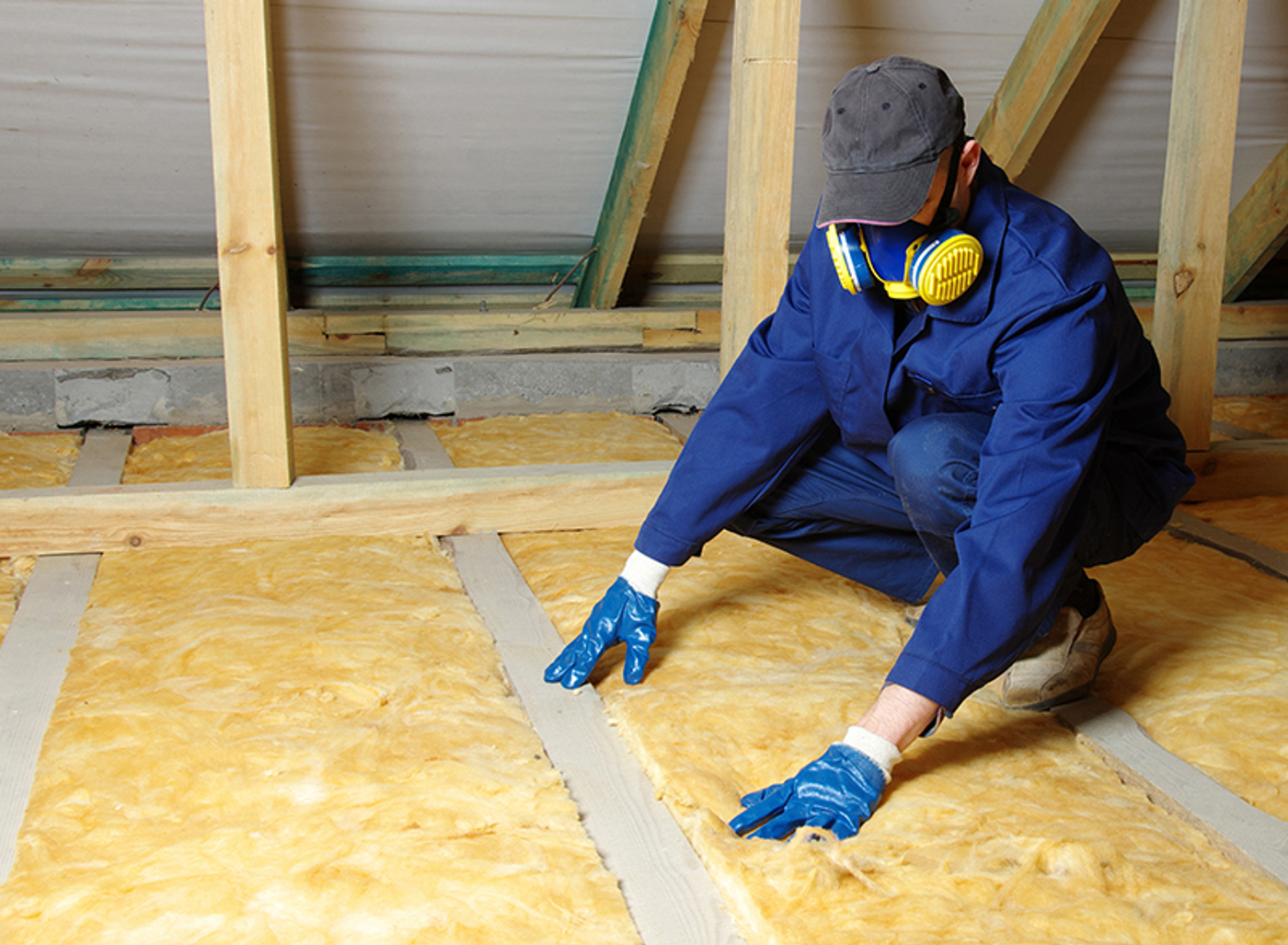
Over a year since the introduction of new H1 insulation standards in New Zealand, we assess the state of play and question the potential impact of rolling these back.
From 1 May 2023 all new building work in New Zealand residential buildings under 300m² has been required to meet H1 wall, floor, and roof insulation performance requirements to enable the efficient use of energy and ensure physical conditions for energy performance. Window and door insulation requirements have also been gradually introduced as part of the staged implementation process, becoming mandatory in November last year.
Debate has been stirring around the continuation of these standards after a Radio New Zealand Official Information Act request revealed Building and Construction Minister Chris Penk MP had raised questions about the standards. Penk addressed these findings in what RNZ called a ‘both sides debate'.
Many in New Zealand’s construction industry, and beyond, were delighted with the introduction of raised standards last year. So, it is unsurprising that any suggestion of a possible backwards step to pre-2023 insulation standards has raised a few brows and prompted a few raised voices.
Expol Commercial Sales Manager, Structural EPS & Foundation Consultant, Wayne Watson has grave concerns about any possible revision of the current standards.
“Prior to 1 May 2023 there was no requirement to insulate a concrete slab unless it was heated, to have new standards introduced that includes all concrete slabs is huge plus for energy efficiency. With this in mind, and the fact that the cost to insulate a slab is minimal, it would be madness to revert back to the old standards for concrete slabs.”
The opinion that the impact the new standards have had in New Zealand, over a year on, is shared by across the industry. Stephen Smith, Technical Director, Knauf Insulation – APAC, says, “The standards are critical for improving the energy efficiency, health, and sustainability of New Zealand homes. While concerns have been raised about the higher costs associated with these new standards, it is important to note that these costs do not need to be as high as claimed if the design stage is managed effectively.
Smith says efficient homes are essential for helping New Zealanders minimise energy costs and cope with the increasing cost of living, as well as these standards being crucial for New Zealand's carbon reduction targets.
He says, since the updated H1 standards were introduced, Knauf Insulation has observed ‘a hugely positive reception for our new range’, which was developed specifically for compliance with the 5th edition of H1. “This positive market response indicates a strong appetite among builders and homeowners for higher performing insulation solutions that contribute to building better, more energy-efficient, and healthier homes in New Zealand,” Smith says.
“Furthermore, the designers we've worked with have acknowledged that the best way to achieve compliance with the new requirements is not simply to use the same designs with higher performing materials. Instead, they have taken time during the design stage to create buildings that achieve compliance without incurring excessive costs. This strategic approach has been instrumental in the acceptance and successful implementation of the new standards.”
Smith is in no doubt that the reversal of these standards would be a detrimental step.
He cites the social impact of enhanced H1 standards being ‘crucial for healthier living environments’, with energy efficiency, environmental commitments also being key factors. He feels economic considerations associated with updated H1 standards can be managed effectively ‘through smart design choices’. “Several builders have demonstrated that careful planning and innovative design can significantly mitigate these costs”
Smith concludes, “Maintaining and building upon the updated H1 standards is vital for ensuring the health, comfort, and well-being of New Zealanders, achieving national carbon reduction goals, and fostering economic growth through innovation. The significant uptake of our energy-efficient products since the introduction of these standards reflects strong market acceptance and the industry's commitment to building better homes.
“Moreover, for manufacturers to invest in New Zealand, there must be certainty of policy. We strongly advocate against rolling back these standards and urge the government to consider the long-term benefits of energy-efficient building practices. Let us continue to move forward towards a more sustainable and resilient future for all New Zealanders, not backwards to condemn millions of New Zealanders to inefficient buildings for years to come.”
Comfortech says it is now seeing most projects being designed to the 5th Edition, 15 months into the H1 change. “Initially the industry favoured a status quo approach of sorts, following the Schedule Method and adapting to the new prescribed higher R values. More recently, as the understanding of the intent of the changes has evolved, we are increasingly seeing designs that utilise the Calculation and Modelling Methods for compliance, enabling a more balanced approach. This has meant adjustments to ceiling and wall insulation R values.”
Products such as the Pink® Superbatts® range including product R values of R 5.0 and R6.0 are finding favour for ceilings, says Comfortech, and increases in wall insulation R values have also been seen over the past year. This has led to Comfortech® developing a secondary wall insulation system that addresses thermal bridging in walls, the company said.
“It has been heartening to see the level of support from industry for the H1 changes, and we believe this is a positive step forward in improving the thermal performance of new homes and meeting New Zealand’s commitments to net zero carbon by 2050.”
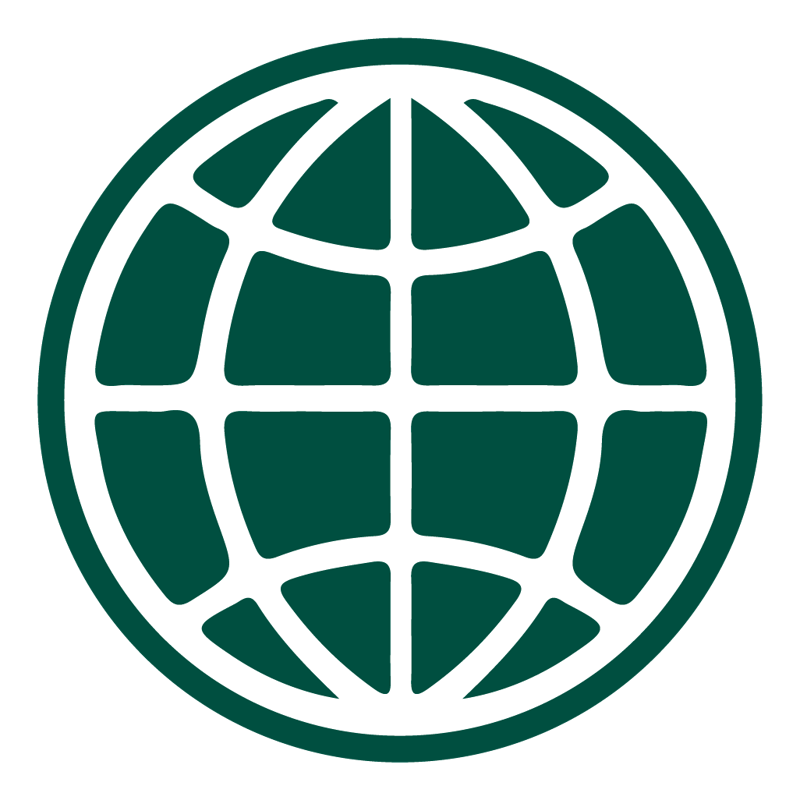