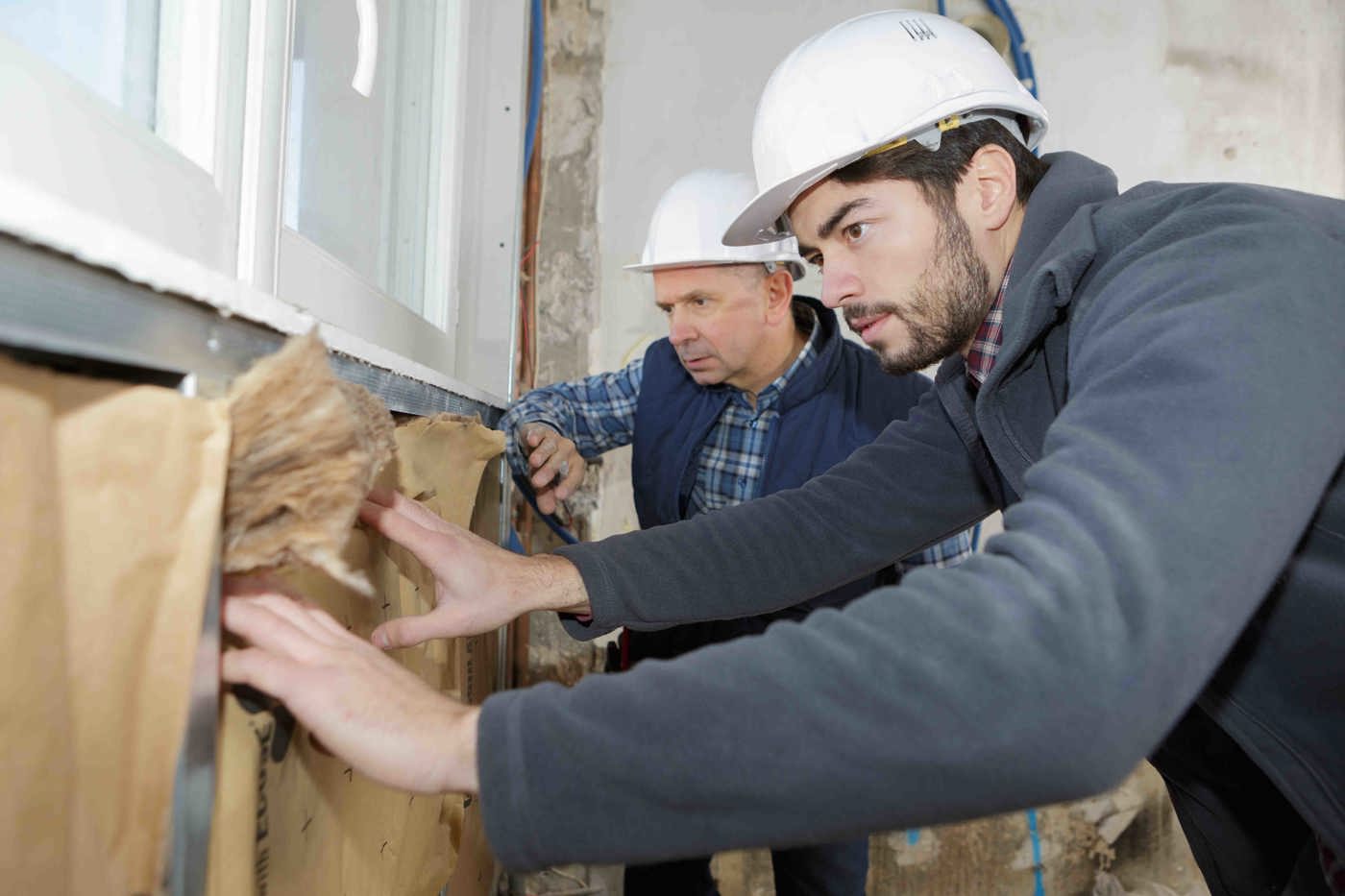
Never has the need for New Zealand to adapt to changing weather patterns been brought more sharply into focus than it has this summer.
As the country counts the cost of an unprecedented clean up and begins to rebuild on a scale not seen before across such a wide area of Aotearoa, changes come into effect to help scale back one of the contributing factors to our warming planet.
The mission to make homes more energy efficient than ever reaches a milestone this May when compliance with the Energy Efficiency (H1) insulation regulations becomes mandatory. The Ministry of Business, Innovation and Employment (MBIE) has updated H1 requirements for insulating new homes and commercial buildings in the New Zealand Building code.
Reducing the amount of energy needed to heat new buildings to make them warmer, drier & healthier, with less impact on the environment, is the aim. Targeted reduction of energy use for residential buildings is approximately 40% and for nonresidential buildings the targeted reduction is 23%.
For now, in the upper North Island (climate zones 1-2), windows and doors continue to require an interim minimum R value of 0.37, as has been the case since 3 November 2022. This will increase to a minimum R value of 0.46 by 2 November 2023.
Construction work in the rest of New Zealand (climate zones 3-6), currently required to reach a minimum R value of 0.37 for all windows and doors, since November, increases to a need for R0.46 (zones 3-4) and R0.50 (zones 5-6) as of May 1 this year.
By 2 November 2023, windows in new housing will be required to meet the increase performance levels for all parts of the country.
Trade Leader approached MBIE for clarification of the requirements, specifically whether wall framing thickness was impacted by the new regulations. An MBIE spokesperson told us, “Under the H1 Energy Efficiency changes, no changes were made to the acceptable solutions in the Building Code that would directly specify the thickness of the wall framing to meet new insulation requirements. The Building Code is a performance based-code and there are many options that can be considered to achieve compliance.”
They went on to explain. “For residential buildings, wall insulation requirements only change slightly and only for the warmer parts of Aotearoa New Zealand. Refer to Table 2.1.2.2B in H1/AS1 and H1/VM1 where the minimum R-value in the Schedule method increased from R1.9 to R2.0. The new R2.0 wall construction R-value of the H1/AS1 Schedule Method is still achievable with common 90 mm wall framing and insulation products.
“Stacking doors may require a deeper wall to accommodate the slightly thicker profiles of thermally-broken joinery. However, this only affects the wall with the stacking door and can be avoided by choosing a different door style.
“For larger buildings other than residential (such as a multistorey commercial building), it is likely that 140 mm framing will be needed to accommodate the new R-values using traditional insulation products and methods. However, typical timber framing for large buildings are generally at least 140 mm deep which would be capable of achieving the new minimum R-values.”
The Building Code provides three methods for compliance:
The Schedule Method – Meet the minimum R-values for building envelope components – roof, windows, external walls and floor.
The Calculation Method – Meet the whole building Heat Loss parameter by calculating overall heat loss from all building envelope elements and allows trading off between elements so you can use higher R-values for some elements than the table shown and lower R-values for others.
The Modelling Method – A calculation of the energy demand for the whole building using whole building calculation software.
In early June 2022, MBIE consulted on a proposed sixmonth extension of the transition period for the insulation requirements in new housing from the 2021 Building Code update. Following the largest number of submissions to any Building Code consultation to date, the compliance date for new wall, floor, and roof insulation requirements for housing
was pushed back from November 2022 to May 2023.
MBIE said this was in recognition of existing pressure on the residential construction sector.
Manager Building Performance and Engineering at MBIE Dr Dave Gittings said, “Response to our consultation showed here is a high level of support for the insulation changes and the need for New Zealand to provide higher performing houses while responding to the urgency of climate change, however parts of the sector told us they needed some more time to prepare for the increase in insulation.”
The amended versions – the Fifth Editions of Acceptable Solution H1/AS1 and Verification Method H1/VM1 – were published on 4 August last year.
As detailed in the Codewords article on page 6, homeowners and the general public are the target audience of Module 1 and Module 2 outlines the different compliance pathways for the requirements.
Homeowners and the general public are the target audience of Module 1, which addresses why building insulation is important to increase energy efficiency and points to the benefits of installing better insulation. It also explains how to identify the climate zones that different parts of the country fall into and background to the new requirements for houses that apply from May.
Module 2 outlines the different compliance pathways for the Building Code’s energy efficiency requirements, including how to choose the appropriate Acceptable Solution or Verification Method for your building work. It covers how to choose the compliance pathway for housing and other building purposes.
Builders will need to ensure they’re abreast of these changes and adapt their building and fabricating practices in line with these. This may include sourcing different building materials as a result.
Commercial lawyer Andrew Skinner says, “We expect builders and fabricators to be in close contact with designers and architects to fully understand the implications of the H1 changes. A failure to pick up the changes when quoting for a job may result in unexpected costs, delays on procuring materials and failed inspections.”
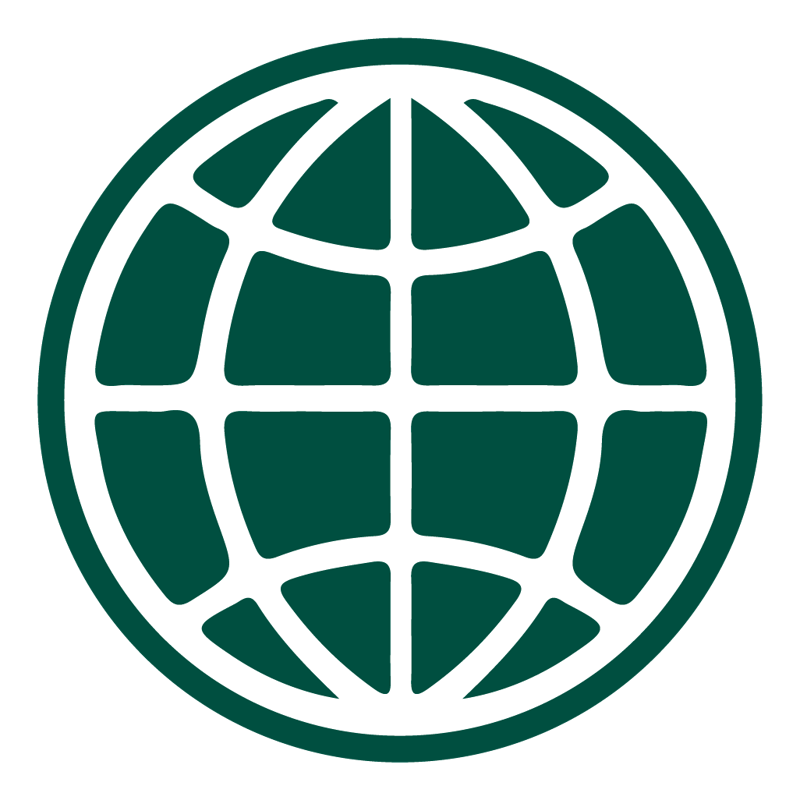