7 Things to consider to reduce fastener popping
As substrate movement is the biggest contributing factor to popping, it’s important to adhere to the following guidelines. The Building Code (see also GIB® Site Guide) requires the moisture content of timber framing to be 18% or less at the time of lining.
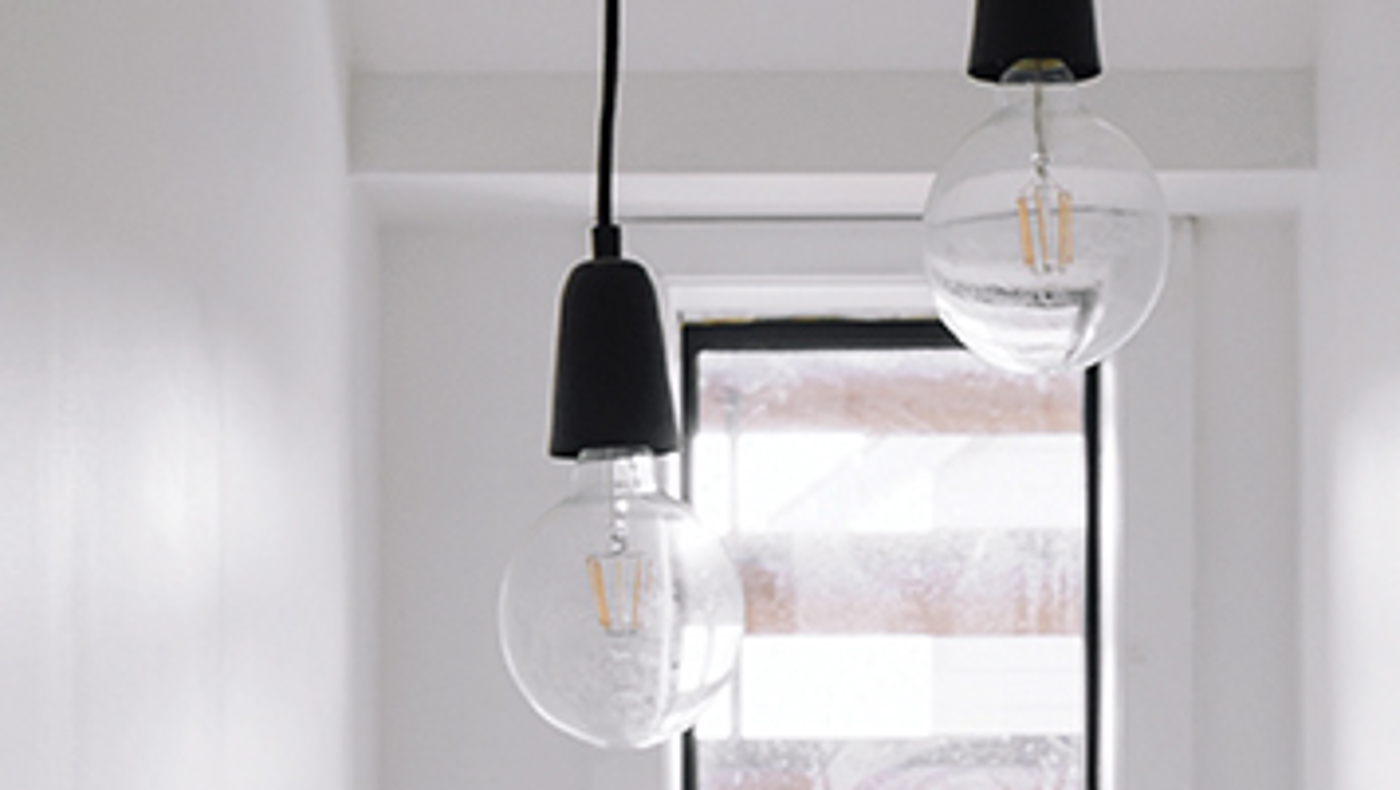
We recommend a lower moisture content (12% or less) if air conditioning, heat pumps or central heating are to be installed; as the equilibrium moisture content of the timber could be as low as 8% once the systems are fully operational.
We know this is a real challenge during wet winter months however, remember that a 3 - 5% moisture change can result in a 1mm dimensional movement in timber. It is therefore essential that the moisture readings are taken accurately and that the timber treatment and temperature ‘correction’ factors are applied to achieve accurate readings.
01. Use metal ceiling batten – They provide a stable substrate for plasterboard ceiling linings as they are nonresponsive to the effects of moisture or humidity. Regular users of metal batten systems consistently have fewer call-backs for movement related ceiling defects such as peaking or cracked joints and popped fasteners.
02. Drive screws in neatly – Overdriven or skewed screws can puncture the face paper which results in no holding power. The head should be neatly seated, slightly below the surface of the sheet.
03. Ensure linings are flush with framing – Whenever the back of the plasterboard is not held tight and secure against the face of the framing substrate by the head of the fastener, a potential fastener pop exists.
04. Fasteners minimum 200mm from adhesive – If fasteners are applied through or adjacent to a daub of adhesive, popping can occur as the adhesive dries and pulls the plasterboardcloser to the framing substrate. Ensure fasteners are fixed a minimum of 200mm from a daub of adhesive.
05. Insert control joints – This is particularly important with large open plan rooms or where corridors enter a large space. As best practice, control joints should be designed and installed wherever there is a risk of structural movement (e.g. large rooms, long walls, entry to large rooms and mid-floor level in stairways).
06. Metal perimeter channel with square stopping for wall/ceiling junction – Where you intend to square stop the wall/ceiling junction, design to replace any nominal 140mm ribbon plate with a conventional 90mm ribbon/top plate so that either a, GIB® Rondo® NZ18 or GIBFix® angle can be fitted to the perimeter. This means the perimeter screws are penetrated into the steel, not the timber. Alternatively, GIB-Cove® will generally cover these at-risk fasteners.
07. Allow adequate drying time – Ensure your winter construction programme accounts for sufficient time for framing to adequately dry steadily and evenly once the building is closed in. While you can’t beat natural airflow, colder months may require the use of artificial heating. LPG burners emit water as a by-product of combustion, this is detrimental to drying of a structure. Where possible use other dehumidifiers or electric heaters. The important consideration is that plasterboard linings should only be installed when the moisture in the timber framing is less than 18% (or lower if air conditioning, heat pumps or central heating are to be installed).
The GIB® Site Guide contains all the information you’ll need to help with installation.
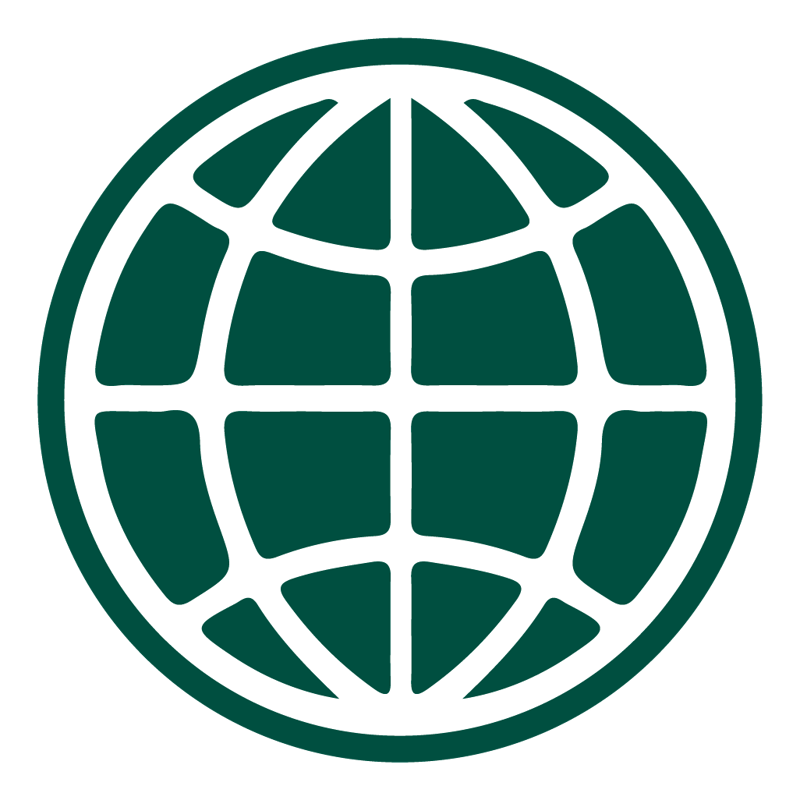